Multi-axis precision motion at the micron or sub-micron level is required in many industrial automation processes as well as in test and metrology applications related to optics, photonics, biotechnology, semiconductor and electronics manufacturing to name a few.
The most common multi-axis motion systems for precision automation consist of 3-axis, motorized linear stages in an XYZ configuration, driven by a closed-loop motion controller with ability to synchronize multi-axis motion with peripheral equipment, such as lasers, cameras, power meters, etc.
DIY vs Professionally Assembled and Calibrated Solutions
Users of such motion systems often ask the question – should I just get the individual components and bolt them together myself, or rather specify a complete XYZ system, mounted, aligned, and tested by a specialist?
As everything in life, the answer depends on the expectations, the performance requirements, and the budget.
L-511-ball-screw based XYZ stage with, absolute encoders, including Z-bracket, XY alignment, assembly, servo tuning, laser calibration / error mapping and performance test documents. The XYZ systems are available in any combination of 2”, 4”, and 6” travel ranges for the X, Y, Z, axes, respectively. The rear view shows the high stability mounting bracket for the Z-axis.
When performance and up-time are critical, it’s worth taking a closer look at what a custom tuned, integrated XYZ motion system can deliver.
Mature System Components
Here, we are focusing on systems based on a modified L-511 precision linear translation stage. The stage is available in three travel ranges - 2”, 4”, and 6” (52mm, 102mm, 155mm) - and has been employed in countless automation applications, so it has reached a very high maturity level.
Why Use Brushless Motors and Absolute Encoders?
Using a brushless motor with integrated absolute rotary encoder provides several advantages. Brushless motors provide very high torque and have no wearing components such as conventional DC motors. They also generate no particles, since no brushes are there to wear over the lifetime.
The absolute encoder eliminates the timely referencing process at start-up, required with conventional incremental encoders. It also provides higher precision and further aids the error mapping process of the stage with the controller during the calibration against a laser interferometer. Also, in case of a power outage, the position information is available immediately, which can be very important when working with delicate, high-value products, such as wafers or optical components.
Why EtherCat® Based Controllers?
The motion systems come calibrated with an A-814 plug-and-play EtherCat®-based industrial motion controller based on ACS components. EtherCat® is an open communication standard with many 3rd party compatible peripherals, such as additional I/O, ADC channels, cameras, etc. Unlike closed, manufacturer-specific communication bus systems, EtherCat® allows for significantly higher flexibility, giving a user more options for future scalability at reduced cost. Adding additional motion channels, for example, is a simple and economic step.
Some of the achievable system highlights are listed below.
- Minimum incremental motion: < 0.5μm
- Absolute accuracy: < ±0.9μm
- Bi-directional repeatability: < ±0.4μm
Test Results
The following graphs show what steps are taken to ensure the overall performance of a custom tuned and calibrated XYZ stage, and achievable results for a system with 4”x4”x4” travel range.
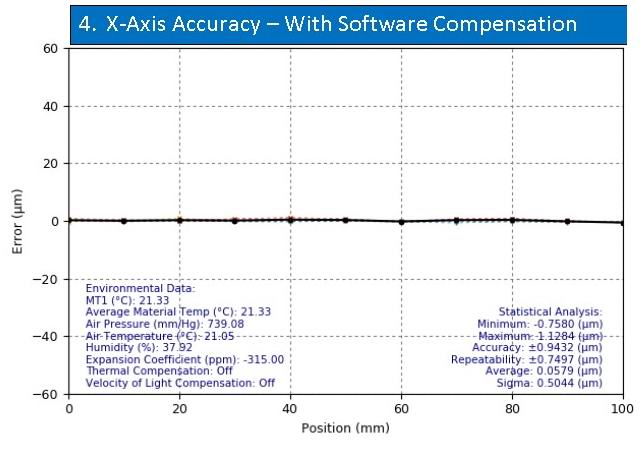
Gantry Multi-Axis Motion Systems
Some multi-axis automation applications require an overhead gantry stage to have access to the complete footprint of the sample or workpiece from above.
There are several options available to satisfy these requirements. A modular approach simplifies the configuration, while still allowing for customization to meet the exacting customer needs. Here, the same A-814 motion controller as shown above can be used. The controller comes with a special gantry control algorithm for enhanced multi-axis precision.
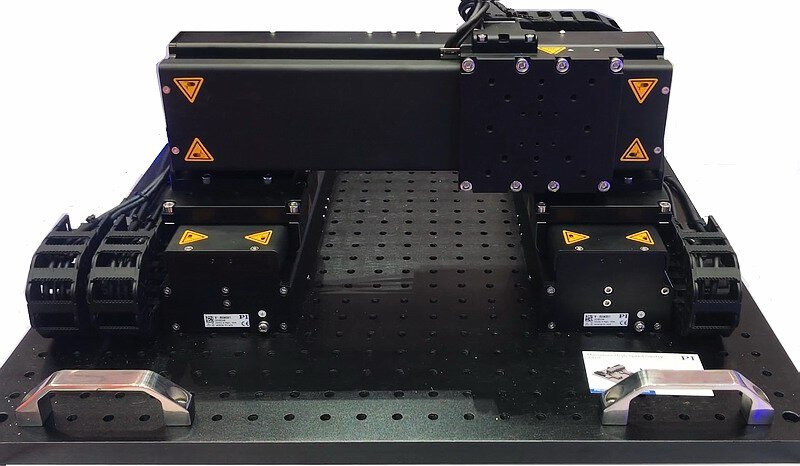
Custom Tuned XYZ Stages and Multi-Axis Assemblies from PI
PI is one of the world leaders in the design and integration of precision positioning stages and motion systems for demanding motion control applications. With many choices - from economical linear stages to high-end air bearing tables and multi-axis gantries - we can offer solutions for industry, OEM and research facilities of all scales.
If you would like more information about our full product range for industrial automation processes, simply contact a member of the PI team directly.