Linearization of the Mechanical System
The linearity of the entire system is one criterion for its positioning accuracy. Piezo actuators typically show a nonlinearity of 10 to 15 %, which has to be compensated by the control loop.
Digital controllers use higher-order polynomials to reduce the motion nonlinearity to values below 0.001 %, which, for a typical travel range of 100 µm, corresponds to an accuracy of one nanometer and better.
Linearization of the Electronics
All digital PI controllers for nanopositioning act the same. This allows any piezo device tuned to a digital control to also be operated by other controllers without any loss of performance. The required comparison data are stored on an ID chip in the stage and called up by the controller prior to start-up.
Dynamic Digital Linearization
In addition, the Dynamic Digital Linearization (DDL) reduces the deviation of repeated periodic trajectories during motion.
This is relevant for scanning applications, where a specific position must be identified and later be approached with high precision, or for applications where a trajectory must be followed for processing steps.
Controllers and Servo Techniques
The task of a servo loop is to correct deviations between the actual position and the target position. Commonly, this is done with proportional and integral controllers with notch filters. However, depending on the application, other control techniques can yield better results in combination with linearization algorithms. Digital filters avoid undesired mechanical excitation, suppress noise and thus increase the resolution of the system.
State Space Control
An alternative control concept is offered for nanopositioning systems: Advanced Piezo Control. This is based on a state space controller which, in turn, is based on a model of the positioning system. Advanced Piezo Control actively dampens the resonance frequency, in contrast to conventional proportional, integral, and differential (PID) controllers with a notch filter, where the mechanical resonance is cut out of the excitation spectrum. The result is faster settling times and a lower sensitivity to external interferences. Phase fidelity is significantly improved compared to damping with one or even two notch filters. This has direct effects on path fidelity and settling behavior.
If the mechanical system has too many resonances close together, or if the resonance frequency to be damped is 1 kHz or more, then the state controller no longer has any advantage over conventional PID controllers in this form. Please discuss your application with us.
Plug-and-Play: ID Chip
The ID chip contains the relevant data of the stage and thus allows fast configuration on the motion controller which supports the ID chip. Depending on the type of drive, the data read out ranges from the type of stage through to individual operating parameters. In the case of piezo-based positioning systems, the best results are achieved by individual comparison of the operating parameters. These depend on the individual stage.
If digital electronics are tuned once, these parameters are stored in the ID chip of the stage. They are therefore automatically available again for operation at a different digital controller, without the need for new adaptation. This exchangeability between stage and controller is a significant step forward for the flexible use of the systems.
Operating Convenience of Digital Controllers
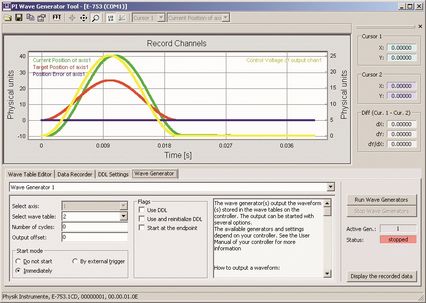
Computing power and memory size which go hand in hand with digital controllers allow useful additional functions to be implemented.
- Software access to all motion parameters and the graphic display of the results
- Coordinate transformation for parallel kinematics for simple control in Cartesian coordinates
- Macro memory to store and retrieve motions which can be triggered externally
- Function generator and waveform memory for the retrieval of predefined trajectories and the generation of customized waveforms
- Data recorders record sensor and control data for subsequent processing
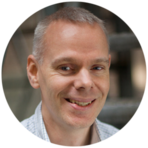
Ask an engineer!
Quickly receive an answer to your question by email or phone from a local PI sales engineer.